Processing of Paints and Coatings with Colloid Mills
Efficient Processing of Paints and Coatings with Colloid Mills from Probst & Class
Probst & Class develop and manufacture colloid mills for the processing of paints and coatings.
Every end product needs its own bespoke machine configuration.
Our strategy for perfect customisation: puclab.
Whether you produce architectural paints, clear high-gloss coats, or scratch-resistant industrial coatings, paint processing places exceptionally high demands on equipment: pigments and fillers must be distributed ultra-finely, particle sizes must stay within tight limits, and the formulation must remain free of entrapped air. Viscosity has to remain stable across the full temperature and shear profile, and foaming must be avoided both in the mixing vessel and on the application roller. PUC colloid mills have been meeting these challenges for decades.
Complete dispersion in a single cycle
The adjustable rotor–stator system in every PUC mill combines cutting, impact, friction and shear forces. Agglomerates are broken down to the sub-micron range in one cycle, reducing both energy consumption and batch times.
Wide viscosity window – from thin-film coatings to trowel-grade pastes
Substances from <100 cP up to 80,000 cP run safely through the mill. Machine size, gap setting and an optional recirculation module adjust the unit precisely to primers, intermediate coats, or top coats.
Process reliability and hygiene
- Sealed packages for water-borne, solvent-borne, and high-strength two-component systems
- Heat- or coolant-jackets prevent skin formation and keep reaction temperatures at set point
- A closed inline process eliminates foam ingress and simplifies subsequent degassing
Complete drainability and quick cleaning
Minimal residual hold-up uses less cleaning fluid and enables faster colour changes with lower scrappage. Polished surfaces and quick-change rotor–stator cartridges shorten cleaning cycles significantly.
Scalable from laboratory to all-out production
Model PUC 60 is suitable for laboratory work; Series O/E deliver up to 34 m³/h, and Series EL up to 80 m³/h. Identical shear geometry across the range guarantees identical results at every scale.
Decades of experience across the process industries
Since 1926, Probst & Class have manufactured colloid mills for virtually every branch of the processing industry—from chemicals, paints and coatings to food, cosmetics, pharmaceuticals and petrochemicals. This breadth of experience is reflected in every design detail, making PUC mills dependable components in both new and existing production lines.
Investment security and low total cost of ownership
PUC have supplied spare and wear parts for decades, regardless of a machine’s year of manufacture. Reliable parts availability, rugged stainless-steel construction, and energy-efficient drives keep your total cost of ownership low and shrink the ecological footprint of your business.
Advantages of paint and coating processing
- Maximum coverage and gloss retention through ultra-fine pigment distribution
- Improved scratch and abrasion resistance via a homogeneous particle matrix
- Reproducible viscosity for reliable application by brush, roller, spray, or coil-coating line
- Rapid colour or product change thanks to complete drainability and easy cleaning
- Low scrappage and reduced solvent consumption
- Long-term spare parts availability secures investment and lowers TCO
- Sustainable closed-loop inline process cuts VOC emissions and energy use
- Seamless scale-up to 80 m³/h with no reformulation required
With a PUC colloid mill you invest in more than a machine—you acquire a powerful, sustainable plant component for the production of modern high-quality paints and coating formulations, from architectural paints right through to high-performance coatings.
Find your ideal machine, reliably and quickly
In the almost 100-year history of Probst & Class, there is one constant: Practically every end product needs its own individual machine configuration!
Two special features of Probst & Class guarantee the highest satisfaction and loyalty of our customers: The simple convertibility of our machines and our approach to customisation.
What has been part of our success for decades is now a strategy. We call this strategy puclab.
puclab is more than a development lab
- System consulting: Holistic concepts for the construction of new systems and the conversion of systems to other products
- Outsourced R&D for our customers' wet grinding, mixing and degassing processes
- Preliminary trials to help decide on the optimal process
- Further development of processes in case of changed specifications
- Application database with test set-ups, test results and videos
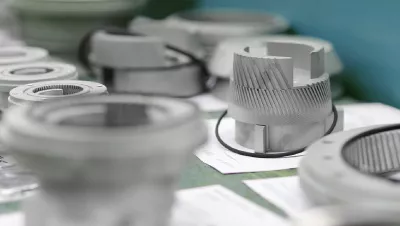
puclab – Pilot
Make an appointment for preliminary tests in our pilot plant.
We give you and your product as much time as needed. Together with your technicians/engineers, we determine the best possible configuration for your new PUC machine in our test lab and plan its integration into your process.

puclab – On-Site
Test a PUC mill in your plant or laboratory.
Talk to our technical support to define the requirements for your process and product. We then provide you with a suitable machine, free of charge, and offer support for your in-house trials.
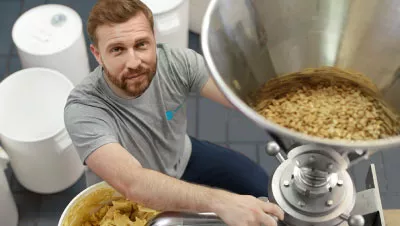
puclab – Remote
Send us your raw materials for testing.
Based on your specifications and materials, we determine the best machine configuration for your end product in our technical centre. Using different grinder sets and settings, we can calculate within a few hours how your new PUC mill needs to be configured, without charge.
Contact our sales department
Still unsure about the best way to proceed?
Simply contact the sales team. We are happy to help you.
- Bitumen Emulsifier: Machines for the Production of Bitumen Emulsion
- Colloid Mills - Try before you buy
- Machines and Colloid Mills for Fungicide Production
- Machines and Colloid Mills for Herbicide Production
- Machines and Colloid Mills for Insecticide Production
- Production of Emulsion Paints with Colloid Mills
- Industrial peanut butter making machine and equipment
- Machines and Colloid Mills for Manufacturing Crop Protection Products
- Machines and components for the production of animal feed
- Machines and industrial equipment for the production of vegan cream
- Machines for grease processing and post-treatment
- Machines for Processing Soybeans
- Machines for the commercial production of facial cream
- Machines for the Industrial Production of Mayonnaise
- Machines for the processing of collagen
- Machines for the production of baby food
- Machines for the production of hand cream
- Machines for the production of jam
- Machines for the production of meat substitutes
- Machines for the production of plant-based cream alternatives
- Machines for the production of plant-based milk alternatives
- Nut mills and machines for nut grinding
- Peanut Processing Machines and Equipment
- Processing of Printing Inks with Colloid Mills
- Processing of Digital Printing Inks with Colloid Mills