Processing of Digital Printing Inks with Colloid Mills
Efficient Processing of Digital Printing Inks with Colloid Mills from Probst & Class
Probst & Class develop and manufacture colloid mills for the processing of digital printing inks.
Every end product needs its own bespoke machine configuration.
Our strategy for perfect customisation: puclab.
Digital printing inks impose stringent demands on process technology: pigments must be dispersed into the sub-micron range without residual agglomerates blocking the printheads; viscosity must remain controllable from low-viscosity inkjet systems up to highly viscous UV pastes; and neither air bubbles nor temperature spikes may arise, because both adversely affect colour stability and tone. PUC colloid mills are engineered precisely for these challenges.
Precise particle-size control in a single cycle
Within the rotor–stator system the product is guided through a continuously adjustable annular gap. Cutting, impact, friction and shear forces act simultaneously, breaking down pigment clusters into the fine range—one event is often enough to reach the target particle size. Cycle times are reduced and over-milling is prevented.
Wide viscosity window – from inkjet inks to effect pastes
All three PUC series process formulations from <100 cP to 80,000 cP. Throughput can be scaled via machine size, gap setting, and—if required—an integrated recirculation module.
Process reliability and hygiene
- Choice of single- or double-acting mechanical seals or PTFE lip seals in one cartridge simplifies changeover between water- and solvent-based formulations
- ATEX-compliant, pharmaceutical, or sterilisable versions plus heat/cool jackets ensure safe handling of both solvent-borne and temperature-sensitive LED-curable inks
- A closed inline layout prevents oxygen and foreign particle ingress, while an optional cooling mantle keeps pigment chemistry stable
Complete drainability and easy cleaning
PUC mills are designed for discharge free of dead space—vertically mounted chambers empty automatically, horizontal versions have low-point outlets. Only a few grams of residue remain, speeding colour changes and minimising waste. All saturated parts are mirror polished and CIP/SIP-capable; rotor–stator sets can be removed, rinsed, or exchanged in minutes.
Scalable from laboratory to high-volume production
Ink development on the PUC 60 lab model starts with identical shear geometry. After scale-up, Series O and E deliver up to 34 m³/h, while EL mills reach 80 m³/h—allowing full formulation series to be transferred reproducibly to production without specification changes.
Ease of operation and maintenance
Frequency inverters, quick-change rotor–stator sets, and lifetime-lubricated precision bearings cut set up and downtimes—vital when frequent colour changes are required.
Decades of cross-industry experience
Since 1926, Probst & Class have supplied colloid mills to virtually every branch of the processing industry—from chemicals, paints and coatings to food, cosmetics, pharmaceuticals and petrochemicals. This wealth of know-how informs every design detail, making PUC mills dependable components in both new and existing production lines.
Investment security and low total cost of ownership
PUC has supplied spare and wear parts for decades, irrespective of a machine’s year of manufacture. Reliable parts availability, robust stainless-steel construction, and energy-efficient drives keep TCO low and shrink the ecological footprint of your business.
Advantages of digital ink processing
- Consistent colour density and brilliance through narrow particle-size distribution
- Fewer nozzle outages thanks to the absence of coarse particles
- Shorter dispersion times—less energy used per kilogram of ink
- Minimal losses during colour changes due to almost complete drainage
- Fast cleaning = higher line availability in multi-product plants
- Long-term parts availability secures investment and keeps TCO low
- Simple scale-up: identical milling principles from the laboratory to the 80 m³/h production line
With a colloid mill from Probst & Class you invest in more than a machine—you acquire a process-secure, sustainable plant component for the manufacture of stable, high-resolution digital printing inks, from photo-realistic inkjet inks through to highly opaque textile pastes.
Find your ideal machine, reliably and quickly
In the almost 100-year history of Probst & Class, there is one constant: Practically every end product needs its own individual machine configuration!
Two special features of Probst & Class guarantee the highest satisfaction and loyalty of our customers: The simple convertibility of our machines and our approach to customisation.
What has been part of our success for decades is now a strategy. We call this strategy puclab.
puclab is more than a development lab
- System consulting: Holistic concepts for the construction of new systems and the conversion of systems to other products
- Outsourced R&D for our customers' wet grinding, mixing and degassing processes
- Preliminary trials to help decide on the optimal process
- Further development of processes in case of changed specifications
- Application database with test set-ups, test results and videos
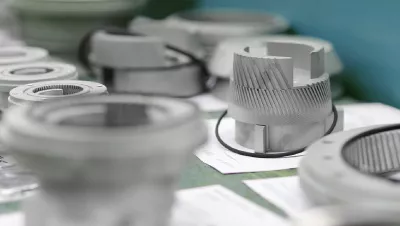
puclab – Pilot
Make an appointment for preliminary tests in our pilot plant.
We give you and your product as much time as needed. Together with your technicians/engineers, we determine the best possible configuration for your new PUC machine in our test lab and plan its integration into your process.

puclab – On-Site
Test a PUC mill in your plant or laboratory.
Talk to our technical support to define the requirements for your process and product. We then provide you with a suitable machine, free of charge, and offer support for your in-house trials.
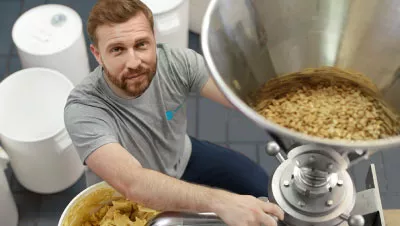
puclab – Remote
Send us your raw materials for testing.
Based on your specifications and materials, we determine the best machine configuration for your end product in our technical centre. Using different grinder sets and settings, we can calculate within a few hours how your new PUC mill needs to be configured, without charge.
Contact our sales department
Still unsure about the best way to proceed?
Simply contact the sales team. We are happy to help you.
- Bitumen Emulsifier: Machines for the Production of Bitumen Emulsion
- Colloid Mills - Try before you buy
- Machines and Colloid Mills for Fungicide Production
- Machines and Colloid Mills for Herbicide Production
- Machines and Colloid Mills for Insecticide Production
- Production of Emulsion Paints with Colloid Mills
- Industrial peanut butter making machine and equipment
- Machines and Colloid Mills for Manufacturing Crop Protection Products
- Machines and components for the production of animal feed
- Machines and industrial equipment for the production of vegan cream
- Machines for grease processing and post-treatment
- Machines for Processing Soybeans
- Machines for the commercial production of facial cream
- Machines for the Industrial Production of Mayonnaise
- Machines for the processing of collagen
- Machines for the production of baby food
- Machines for the production of hand cream
- Machines for the production of jam
- Machines for the production of meat substitutes
- Machines for the production of plant-based cream alternatives
- Machines for the production of plant-based milk alternatives
- Nut mills and machines for nut grinding
- Peanut Processing Machines and Equipment
- Processing of Paints and Coatings with Colloid Mills
- Processing of Printing Inks with Colloid Mills