Machines for the production of hand cream
Machines for the production of hand cream:
Probst & Class develop and manufacture both individual components and complete systems for the homogenisation, emulsification and deaeration of hand cream.
Every end product needs its own bespoke machine configuration.
Our strategy for perfect customisation: puclab.
Raw materials for the production of hand cream
The following raw materials and preliminary products are used in the production of hand creams:
- Water
- Oils and fats
- Emulsifiers
- Humectants
- Thickening agents
- Active ingredients
- Fragrances and colourings
- Preservatives
- Special additives
Process steps in the production of hand cream
The production process begins with weighing or measuring the volume of the desired ingredients. If necessary, oils and fats are heated in advance to achieve a liquid phase. All the ingredients of the aqueous phase and the oil phase are then mixed together though separately. The two phases are then combined during emulsification to create an emulsion. The emulsion is then homogenised further. The emulsifying and homogenising processes are carried out in one or more procedures using colloid mills or similar rotor-stator systems.
Advantages of our colloid mills in the production of hand cream
Colloid mills from Probst & Class use high shear and centrifugal forces to produce very fine particles, in particular homogeneous emulsions. Homogeneous emulsions are less susceptible to unwanted phase separation or segregation. Our colloid mills can process large production quantities efficiently with low energy consumption. With 80 years of experience and R&D in the engineering of rotor-stator systems, we can offer our customers the optimal machine configuration for almost any application.
Advantages of our vacuum degassing systems
With our deaerators (vacuum deaeration machines), air can be removed from the product before packaging, which significantly improves the quality and shelf life of the end product.
Probst & Class as a supplier to the cosmetics industry
Probst & Class mills have been used in state-of-the-art cosmetics processing for 80 years. With a PUC, both small and large companies produce cosmetics of top quality consistently.
The high production quality of PUC machines usually guarantees a service life of several decades. The supply of spare and wear parts, even for very early models, guarantees a secure investment and low total cost of ownership.
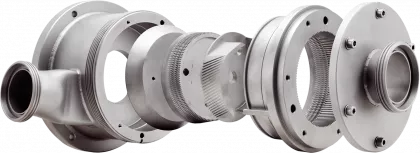
Find your ideal machine, reliably and quickly
In the almost 100-year history of Probst & Class, there is one constant: Practically every end product needs its own individual machine configuration!
Two special features of Probst & Class guarantee the highest satisfaction and loyalty of our customers: The simple convertibility of our machines and our approach to customisation.
What has been part of our success for decades is now a strategy. We call this strategy puclab.
puclab is more than a development lab
- System consulting: Holistic concepts for the construction of new systems and the conversion of systems to other products
- Outsourced R&D for our customers' wet grinding, mixing and degassing processes
- Preliminary trials to help decide on the optimal process
- Further development of processes in case of changed specifications
- Application database with test set-ups, test results and videos
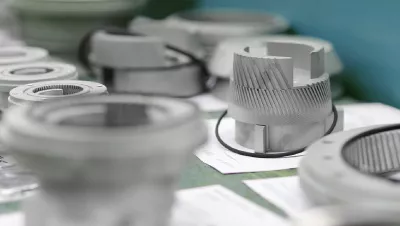
puclab – Pilot
Make an appointment for preliminary tests in our pilot plant.
We give you and your product as much time as needed. Together with your technicians/engineers, we determine the best possible configuration for your new PUC machine in our test lab and plan its integration into your process.

puclab – On-Site
Test a PUC mill in your plant or laboratory.
Talk to our technical support to define the requirements for your process and product. We then provide you with a suitable machine, free of charge, and offer support for your in-house trials.
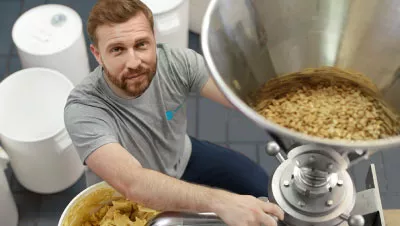
puclab – Remote
Send us your raw materials for testing.
Based on your specifications and materials, we determine the best machine configuration for your end product in our technical centre. Using different grinder sets and settings, we can calculate within a few hours how your new PUC mill needs to be configured, without charge.
Contact our sales department
Still unsure about the best way to proceed?
Simply contact the sales team. We are happy to help you.
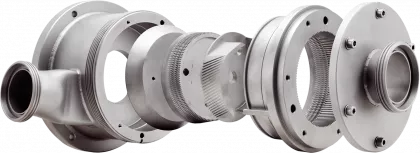
- Bitumen Emulsifier: Machines for the Production of Bitumen Emulsion
- Colloid Mills - Try before you buy
- Machines and Colloid Mills for Fungicide Production
- Machines and Colloid Mills for Herbicide Production
- Machines and Colloid Mills for Insecticide Production
- Production of Emulsion Paints with Colloid Mills
- Industrial peanut butter making machine and equipment
- Machines and Colloid Mills for Manufacturing Crop Protection Products
- Machines and components for the production of animal feed
- Machines and industrial equipment for the production of vegan cream
- Machines for grease processing and post-treatment
- Machines for Processing Soybeans
- Machines for the commercial production of facial cream
- Machines for the Industrial Production of Mayonnaise
- Machines for the processing of collagen
- Machines for the production of baby food
- Machines for the production of jam
- Machines for the production of meat substitutes
- Machines for the production of plant-based cream alternatives
- Machines for the production of plant-based milk alternatives
- Nut mills and machines for nut grinding
- Peanut Processing Machines and Equipment
- Processing of Paints and Coatings with Colloid Mills
- Processing of Printing Inks with Colloid Mills
- Processing of Digital Printing Inks with Colloid Mills