Bitumen Emulsifier: Machines for the Production of Bitumen Emulsion
Bitumen Emulsifier: Machines for the Production of Bitumen Emulsions
Probst & Class develop and manufacture colloid mills for the production of bitumen emulsions.
Every end product needs its own bespoke machine configuration.
Our strategy for perfect customisation: puclab.
Emulsification Process (Bitumen in Water)
The production of bitumen emulsions is preferably carried out in colloid mills, which have been built by Probst & Class for decades and have proven themselves in the petrochemical industry.
The emulsification of bitumen in water is achieved by intensive mixing in the presence of an emulsifier. This process can occur either batch-wise (batch process) or continuously (in-line process), with a colloid mill usually providing the required mixing. During the process, the aqueous phase and bitumen pass through the colloid mill, where emulsification occurs.
Adjustable pumps (metering pumps) are used to transfer the aqueous phase and bitumen to the colloid mill.
The aqueous phase contains, besides water, the emulsifier, acid (or base), and, if necessary, a stabiliser, all of which are carefully balanced in quantity. Bitumen is used either pure or mixed with a solvent. The hot emulsion is pumped into a storage tank and kept there for filling and delivery.
The temperature of the emulsion must never reach 100°C during production but should be maintained between 85°C and 95°C. To avoid overheating, the temperature of the bitumen and aqueous phase should be well-coordinated.
Recipe Development in the Laboratory with Colloid Mills from Probst & Class
The application possibilities of bitumen emulsions and the quality demands of customers are high. Therefore, bitumen producers are moving towards developing optimal formulations in the laboratory. Our colloid mill model 60 / O is particularly suitable for this task.
For the development of bitumen formulation, the machine is equipped with a double-jacket housing and double-jacket funnel, as well as a circulation line with a discharge valve.
A circulating thermostat is used for heating and cooling the machine. The working temperature can be selected from the range of 20°C to 250°C. To ensure reproducibility for production conditions, the use of a frequency converter is recommended. For modified bitumen, we provide the corresponding emulsification tools.
Production of Bitumen Emulsion in In-line Operation
In continuously operating plants, preparation tanks for the aqueous and bitumen phases are omitted. All components used are taken directly from storage tanks. The aqueous phase is prepared so that emulsifier, acid and stabiliser are fed into the water stream in predetermined quantities. This is done in such a timely manner that the reaction between the emulsifier and acid occurs before the entire water phase enters the colloid mill.
Water is heated in a heat exchanger. The precise dosing of emulsifier and acid is monitored by a pH electrode installed directly before entering the colloid mill.
Bitumen and solvents are also continuously fed into the colloid mill. The bitumen is stored at the correct temperature, so no further temperature control is required.
Production of Bitumen Emulsion in Batch Operation
In a batch operation, the aqueous phase and bitumen phase are prepared in separate containers and brought to the required temperatures. The fill levels are chosen so that, after combining both phases, an emulsion with the desired bitumen content is achieved. Usually, the containers have level indicators that allow for accurate reading of the outgoing liquid amounts at all times. In this case, the use of metering pumps is unnecessary. Simple pumps can be used instead.
The aqueous phase and bitumen pass through the colloid mill until both storage containers are empty. Since the quantities of bitumen and aqueous phase are precisely prepared, the produced emulsion must meet the content requirements of the bitumen.
Occasionally, bitumen taken from the storage tank is fed directly into the colloid mill. In this case, precise control of the flow rates of bitumen and the aqueous phase is necessary. This is possible through the regulation of metering pumps or with the help of automatic control devices.
Probst & Class as a Supplier to the Petrochemical Industry
Probst & Class mills are "state-of-the-art" machines that have been used in the petrochemical industry for 80 years. Using a PUC, both small outfits and large industrial companies produce bitumen emulsions of consistently highest quality.
The high manufacturing quality of PUC machines typically ensures a service life of several decades. The supply of replacement and spare parts, even for very early models, guarantees a secure investment and low total cost of ownership over the entire life cycle of the machines.
Find your ideal machine, reliably and quickly
In the almost 100-year history of Probst & Class, there is one constant: Practically every end product needs its own individual machine configuration!
Two special features of Probst & Class guarantee the highest satisfaction and loyalty of our customers: The simple convertibility of our machines and our approach to customisation.
What has been part of our success for decades is now a strategy. We call this strategy puclab.
puclab is more than a development lab
- System consulting: Holistic concepts for the construction of new systems and the conversion of systems to other products
- Outsourced R&D for our customers' wet grinding, mixing and degassing processes
- Preliminary trials to help decide on the optimal process
- Further development of processes in case of changed specifications
- Application database with test set-ups, test results and videos
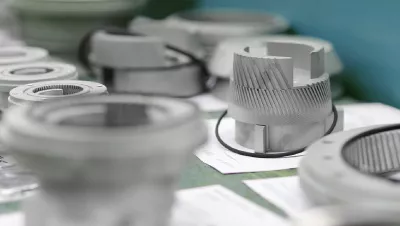
puclab – Pilot
Make an appointment for preliminary tests in our pilot plant.
We give you and your product as much time as needed. Together with your technicians/engineers, we determine the best possible configuration for your new PUC machine in our test lab and plan its integration into your process.

puclab – On-Site
Test a PUC mill in your plant or laboratory.
Talk to our technical support to define the requirements for your process and product. We then provide you with a suitable machine, free of charge, and offer support for your in-house trials.
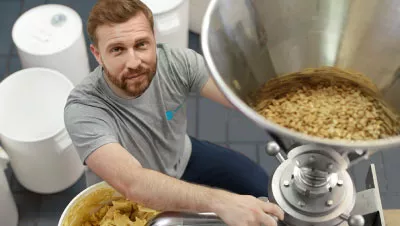
puclab – Remote
Send us your raw materials for testing.
Based on your specifications and materials, we determine the best machine configuration for your end product in our technical centre. Using different grinder sets and settings, we can calculate within a few hours how your new PUC mill needs to be configured, without charge.
Contact our sales department
Still unsure about the best way to proceed?
Simply contact the sales team. We are happy to help you.
- Colloid Mills - Try before you buy
- Machines and Colloid Mills for Fungicide Production
- Machines and Colloid Mills for Herbicide Production
- Machines and Colloid Mills for Insecticide Production
- Production of Emulsion Paints with Colloid Mills
- Industrial peanut butter making machine and equipment
- Machines and Colloid Mills for Manufacturing Crop Protection Products
- Machines and components for the production of animal feed
- Machines and industrial equipment for the production of vegan cream
- Machines for grease processing and post-treatment
- Machines for Processing Soybeans
- Machines for the commercial production of facial cream
- Machines for the Industrial Production of Mayonnaise
- Machines for the processing of collagen
- Machines for the production of baby food
- Machines for the production of hand cream
- Machines for the production of jam
- Machines for the production of meat substitutes
- Machines for the production of plant-based cream alternatives
- Machines for the production of plant-based milk alternatives
- Nut mills and machines for nut grinding
- Peanut Processing Machines and Equipment
- Processing of Paints and Coatings with Colloid Mills
- Processing of Printing Inks with Colloid Mills
- Processing of Digital Printing Inks with Colloid Mills